Noah Cable’s olive oil is MIA.
Well, not exactly missing in action. He knows roughly where it is. It’s in a 20-foot shipping container that left Italy in August. In a normal year, it would have reached his shelves in July.
Cable is one of the owners of Wellspent Market, a specialty food business in Portland. Olive oil is the backbone of their business. (His partner Jim Dixon’s Twitter handle is @pdxoliveoilguy.) But their big, annual shipment of Italian oil is months delayed.
So, Cable waits. He logs onto the website vesselfinder.com to track the boat carrying the olive oil. He does that a lot. Sometimes he checks on his phone.
“It’s like watching your shoes come that you ordered online,” he said. “I’m literally going onto the website every day and being like, OK where are you now?”
Wellspent Market is one of many businesses in Oregon snarled in the global supply chain disruptions wrought by the pandemic — from toilet paper last spring to microchips today. These disruptions have hurt businesses small and large. Sportswear giant Nike, headquartered near Beaverton, recently cut its revenue forecast after a COVID-19 surge shuttered footwear factories in Vietnam.
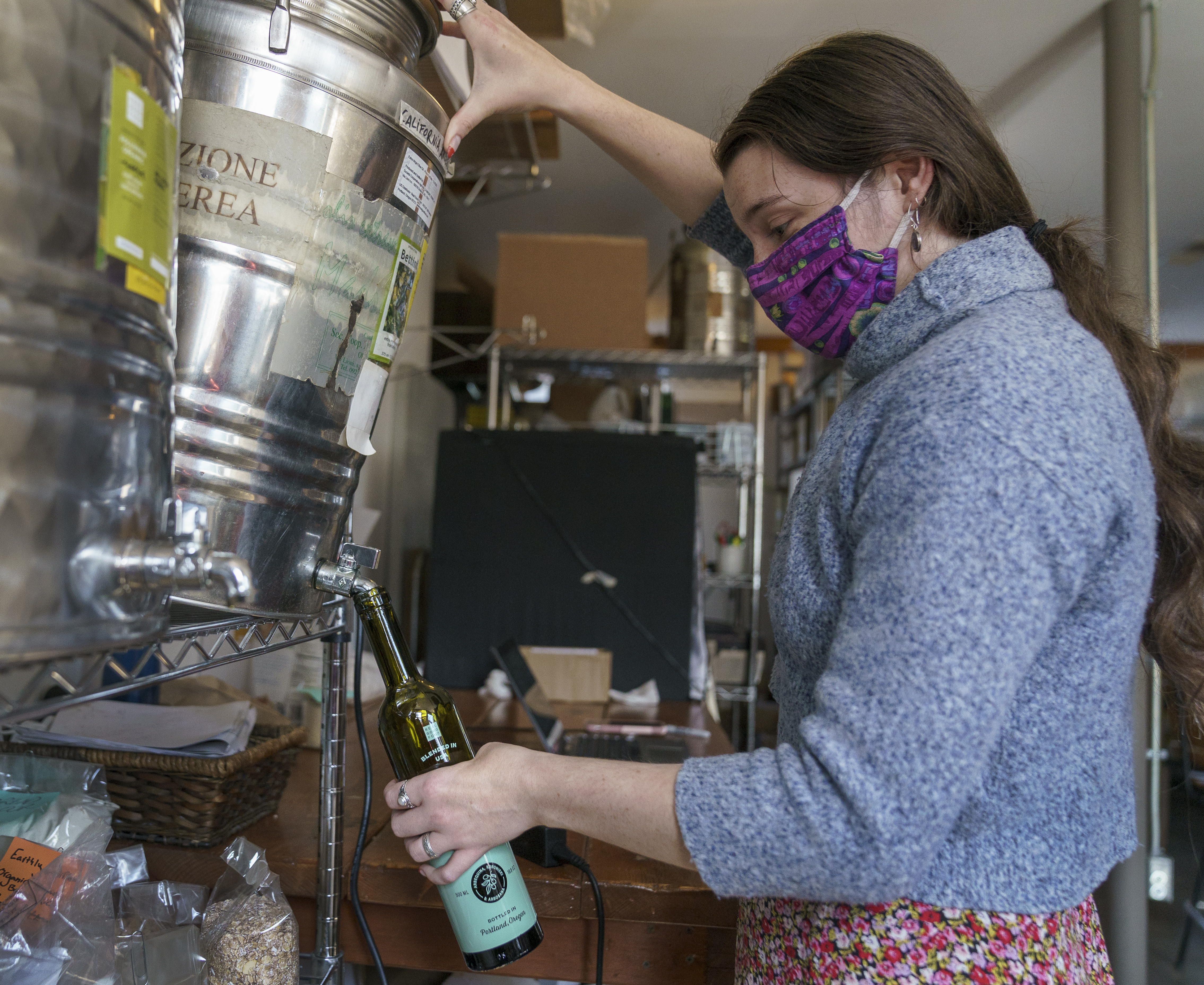
Kristyna Wentz-Graff / OPB
But when it comes to small businesses — well, they want to grow. And supply chain troubles have gone on so long they’ve constrained the growth of smaller outfits such as Wellspent Market.
How olive oil delays changed a company’s growth curve
The olive oil is a case in point. It was delayed getting from farms to shipping container. Then delayed again getting on a boat to leave Italy. Cable watched, on the vesselfinder.com map, as the container ship carrying it crossed the Panama Canal and made its way past Manzanillo, Mexico. He followed as that boat made it through the Port of Long Beach. Some Southern California ports have been parking lots, with vistas of container ships idled in wait.
At some point, though, the olive oil was loaded onto a different ship heading to Seattle. It’s expected to reach port by next week, though it will likely be November before the oil gets trucked down to Portland.
Meanwhile, there’s a lot of cash tied up in that shipping container.
“It’s almost $100,000 worth of olive oil,” Cable said. “Which I can’t stress enough is a massive amount of outlay of cash to just be sitting for months on end.”
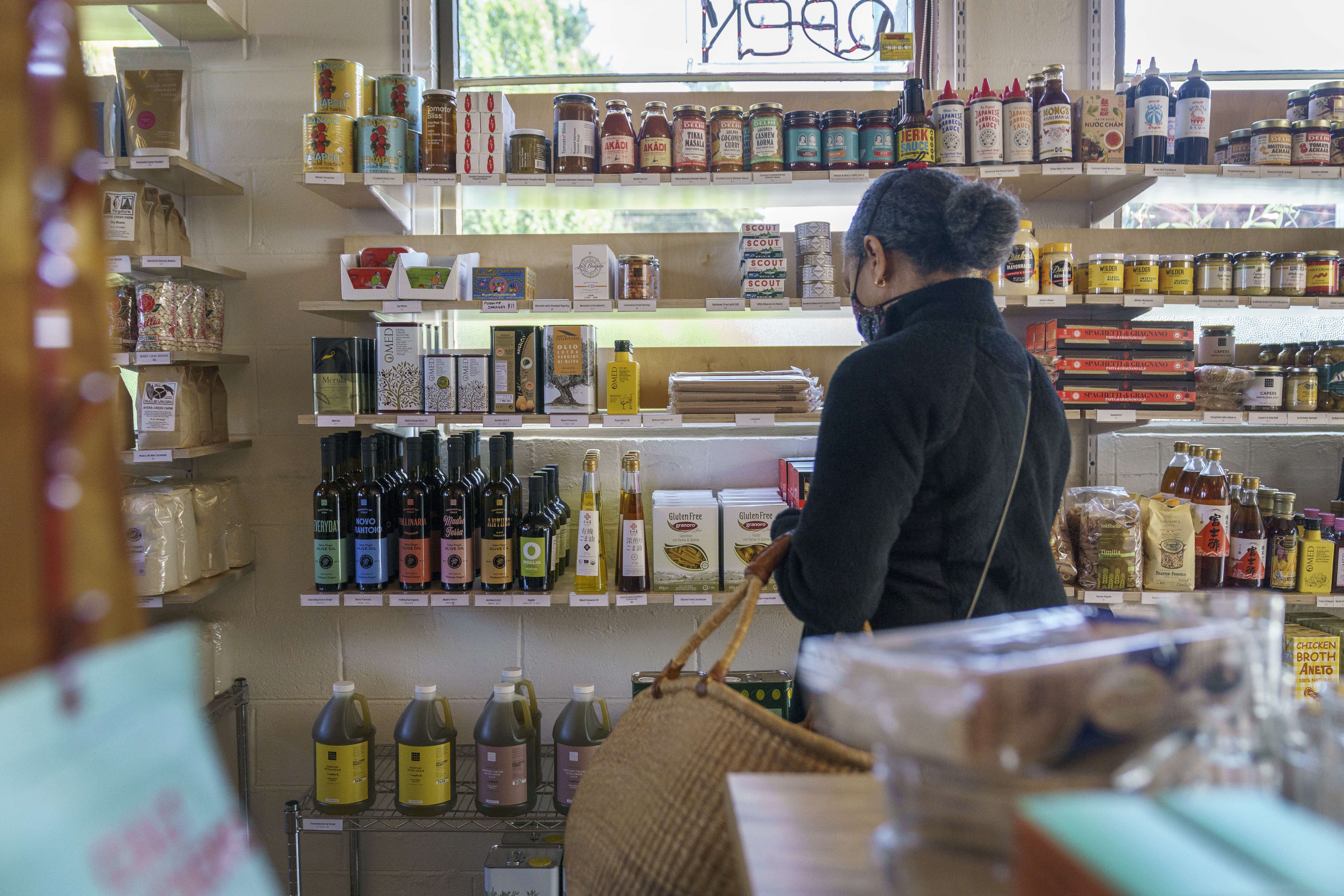
Kristyna Wentz-Graff / OPB
The delay has hobbled one of Cable’s growth plans — at least for now. He had planned to launch a distribution program that would put Wellspent’s olive oil in more local shops. He wanted the program flourishing by the holidays.
But with the oil arriving halfway through November…
“That entire program is on hold.”
The big picture: Everybody feels the pain
In some respects, Oregon’s economy may have had less direct exposure to supply chain issues than other states because of industries that rely on locally sourced products.
“So, the wine industry or the dairy industry or the lumber industry. Those industries, by definition, are more resilient, because they’re less connected to the global supply chain, at least at the supply side,” said Carlos Mena, a professor of supply chain management at Portland State University.
Still, Mena said, every company ends up feeling the effects in some way — either directly through shortages or indirectly through inflation as prices go up.
In the end, everybody feels the pain, said Josh Lehner, an economist with the state of Oregon.
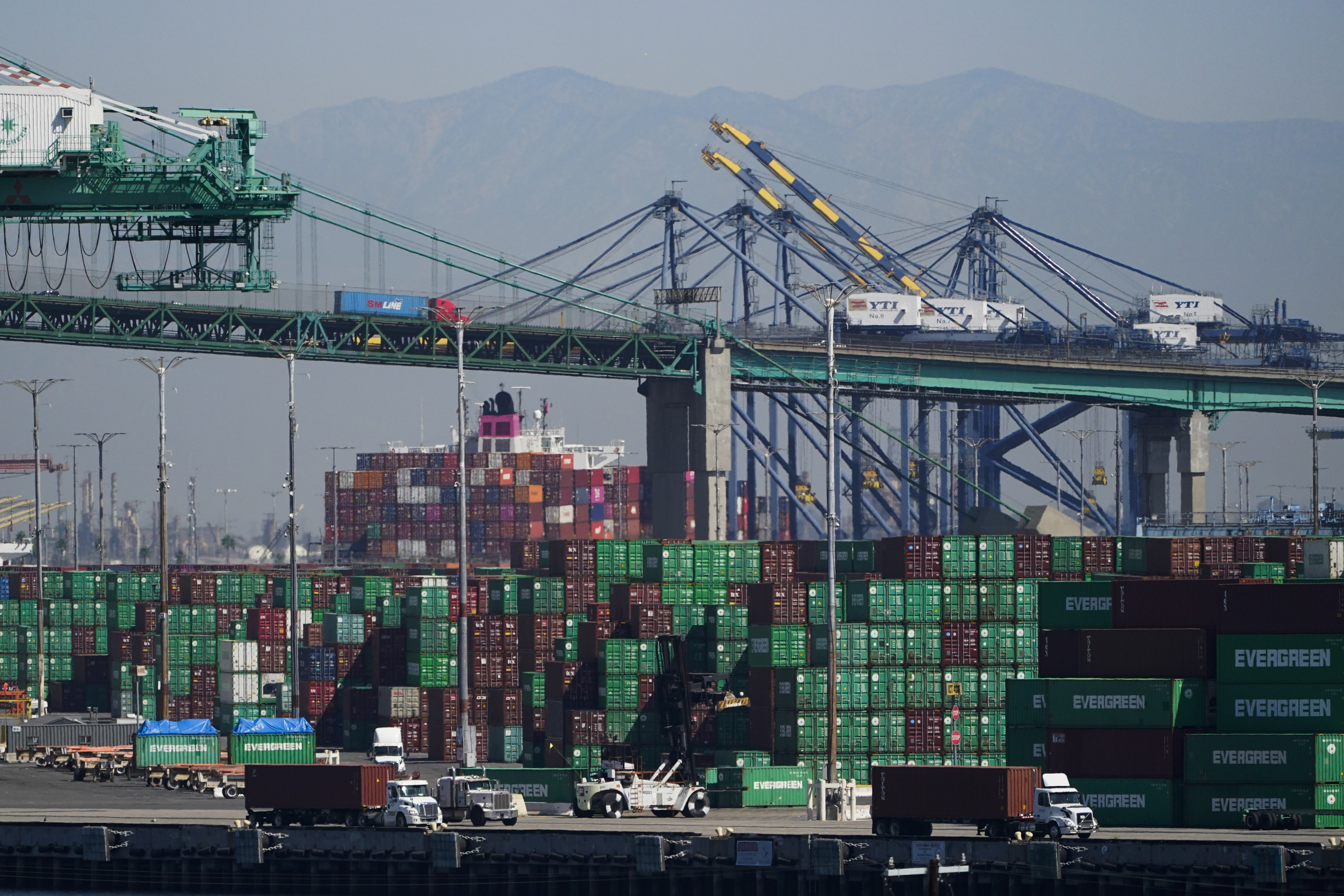
Jae C. Hong / AP
“We have global supply chains in every single industry,” he said. “And so, when you have problems at the ports in Southern California or the railyards in the Midwest or we’re running out of raw materials over in Southeast Asia and the like, those reverberate throughout the economy.”
Even companies with home-grown products are not immune. Take Westward Whiskey, the largest whiskey producer in Oregon. It’s been called “Oregon’s single malt powerhouse.”
During the pandemic, that powerhouse has been pinched by bottle shortages.
Paying a price for the bottle bottleneck
Westward makes its whiskey from Northwest grain. But its angled bottles are custom made for the brand in Mexico.
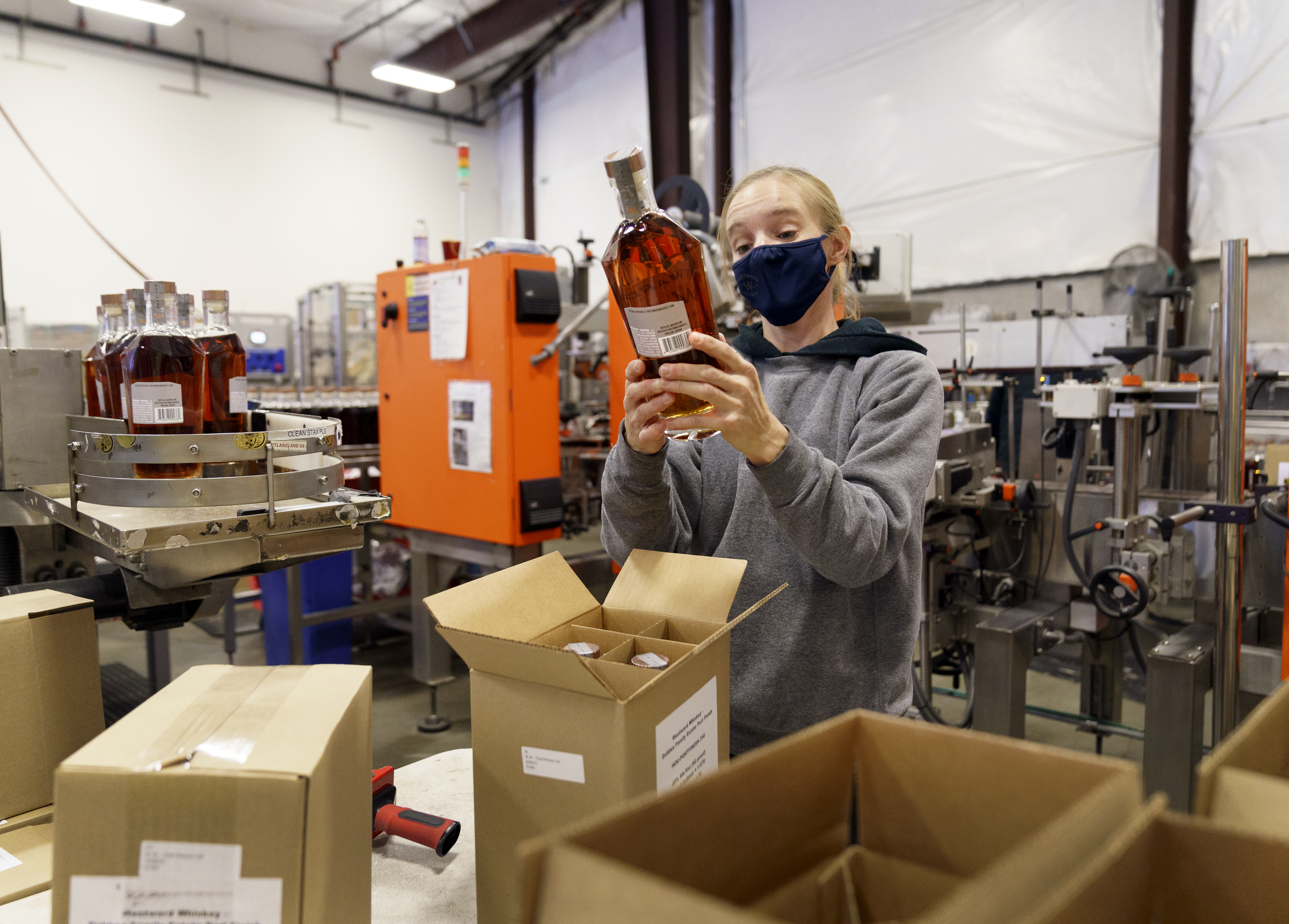
Kristyna Wentz-Graff / OPB
Thomas Mooney, Westward’s co-founder and CEO, said supply chain disruptions, including bottle shortages, have been a nightmare.
“Every step of everything that is supply chain related has been a battle,” he said. “And that is certainly not getting better.”
The bottle factory in Mexico City has endured its own supply chain problems. Mooney said one of its production leaders died from COVID-19 — a trauma that compounded the difficulty of operating a factory in the pandemic.
While it used to take several months to order and receive bottles, Mooney said it can now take three times that long.
“It feels like there hasn’t been a week in the last 18 months when we weren’t short of one of our bottle sizes,” he said. “Running out of a bottle size is not just an annoyance. It makes it impossible to do business in a market.”